Key Quality Documents to Prepare at the Start of a Construction Project
- raimondpsantos
- Oct 5, 2024
- 3 min read
Updated: Oct 7, 2024
In construction projects, quality management plays a crucial role in ensuring that the project meets the required standards and specifications. At the outset, having well-prepared quality documents not only sets the tone for a smooth execution but also ensures compliance with regulatory requirements, client specifications, and industry standards. Below are essential quality documents that every project should have in place from the start.
1. PROJECT QUALITY PLAN (PQP)
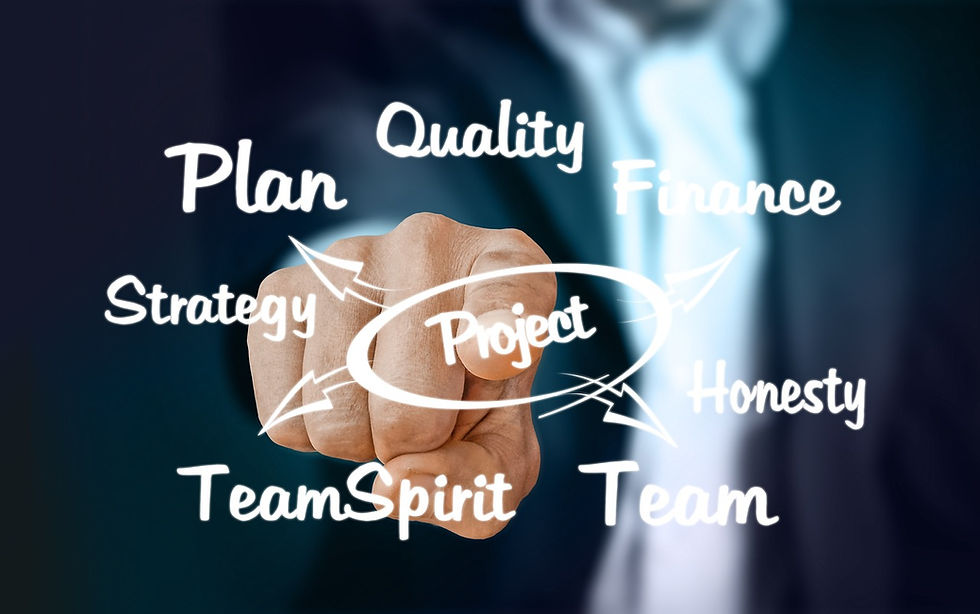
The Project Quality Plan is the cornerstone of quality management in a construction project. It outlines the procedures, processes, and quality assurance measures that will be implemented throughout the project. The PQP typically includes:
Project scope and objectives – Describes the project's purpose and key deliverables.
Roles and responsibilities – Defines the roles of quality personnel, site engineers, and contractors.
Inspection and testing procedures – Identifies the checks that will be performed on materials, equipment, and construction processes.
Non-conformance management – Details how non-conformances will be identified, corrected, and prevented.
Document control – Specifies how project documents will be stored, updated, and distributed.
This document serves as a reference for the entire project team to ensure everyone is aligned on quality expectations.
2. LIST OF TESTS
A comprehensive list of tests ensures that the materials and construction works meet the required standards. This list should include:
Type of test – E.g., concrete compressive strength, soil compaction, etc.
Testing criteria – Reference to standards like ASTM, BS, or project-specific guidelines.
Frequency of tests – Specifies how often tests should be performed (e.g., after every 50 cubic meters of concrete placement).
Acceptance criteria – Outlines the acceptable range of test results.
This document helps maintain consistency and ensures that all tests are performed at the right intervals, following specific guidelines.
3. LIST OF MATERIALS
Before starting the work, all materials that will be used in the project must be reviewed and approved. The List of Materials for Approval includes:
Material description – E.g., type of cement, steel reinforcement, tiles, etc.
Supplier details – Information about the manufacturer or supplier.
Specification references – Standards or specifications that the material adheres to.
Approval status – Records whether the material has been approved or is still pending.
This document ensures that only approved materials conforming to the project’s specifications are used.
4. LIST OF METHOD STATEMENTS
Method statements are detailed, step-by-step instructions on how specific tasks or construction activities will be carried out. A List of Method Statements is crucial as it outlines:
Description of activities – E.g., excavation, formwork installation, concrete pouring, etc.
Safety precautions – Safety measures for workers and equipment to avoid accidents.
Equipment and manpower required – Resources needed for task completion.
Quality checks and approvals – Ensures the method meets both quality and safety standards.
By ensuring that method statements are properly prepared and followed, teams can avoid rework and ensure compliance with quality and safety standards.
5. WORK INSPECTION REGISTER
The WIR register is a key document that tracks the various inspections required during the project. It includes:
Inspection types – E.g., foundation inspections, formwork checks, etc.
Inspection schedule – Date and time of each inspection.
Approval stages – Tracks the status of each inspection (approved, pending, or rejected).
This register serves as a roadmap for quality inspections, ensuring that all required inspections are completed in a timely manner.
6. ENGINEERING DELIVERABLES
Technical drawings provide the blueprint for the project’s execution. The List of Technical Drawings ensures that all necessary designs are available and reviewed before work begins. It typically includes:
Drawing number and title – E.g., "Structural layout," "Electrical wiring diagram," etc.
Date of issue – The latest version of the drawing.
Approval status – Notes whether the drawing has been approved for construction.
This list ensures that only the latest and approved drawings are used during construction, reducing the risk of errors and rework.
Starting a construction project with well-prepared quality documents is crucial for ensuring success. The Project Quality Plan, List of Tests, List of Materials for Approval, List of Method Statements, Work Inspection Request Register, and Engineering deliverables provide the framework for achieving consistent quality throughout the project lifecycle. By putting these documents in place early on, you can set your project up for smooth execution, fewer mistakes, and timely completion while meeting all quality requirements.
Comments