Common Quality Terms in Construction
- raimondpsantos
- Feb 11, 2022
- 7 min read
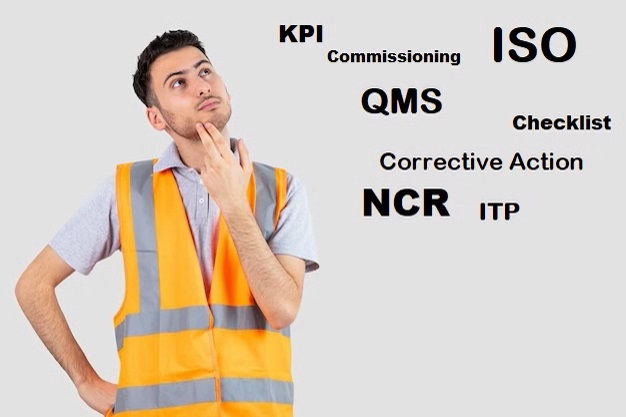
Here are some quality common terms used in the construction industry:
Acceptance Criteria - is the quality provision of technical basis and conditions that used to determine whether goods or services are accepted or satisfied by a user or customer.
Calibration Certificate – is a document that contains information about a device’s calibration. This certificate provides valuable information on the quality and measurement accuracy of the device.
Check sheet - A simple data-recording device. The check sheet is custom designed for the particular use, allowing ease in interpreting the results. The check sheet is one of the seven tools of quality. Check sheets should not be confused with data sheets and checklists.
Checklist - A tool for organizing and ensuring that all important steps or actions in an operation have been taken. Checklists contain items that are important or relevant to an issue or situation. Checklists should not be confused with check sheets and data sheets.
Commissioning - refers to the process of bringing an item into operation and ensuring that it is in good working order. On building projects, this refers primarily to building services.
Continual Improvement - is the ongoing improvement of products, services or processes through incremental and breakthrough improvements. These efforts can seek "incremental" improvement over time or "breakthrough" improvement all at once.
Corrective Action – is an aspect of quality management that aims to rectify a task, process, product, or even a person’s behavior when any of these factors produce errors or have deviated from an intended plan. Corrective actions can be thought of as improvements to an organization to eliminate undesirable effects.
Customer Satisfaction - Customer satisfaction is defined as a measurement that determines how happy customers are with a company’s products, services, and capabilities. Customer satisfaction information, including surveys and ratings, can help a company determine how to best improve or changes its products and services.
FAT (Factory Acceptance Test) - Factory Acceptance Testing (FAT) helps verify that newly manufactured and packaged equipment meets its intended purpose. The FAT validates the operation of the equipment and makes sure the customers’ purchase order specifications and all other requirements have been met.
IMS (Integrated Management System) – An IMS integrates all of an organization’s systems and processes into one complete framework, enabling an organization to work as a single unit with unified objectives.
Inspection Request - is a quality control document that is submitted by the contractor to the consultant. If the consultant approves the Inspection Request then that particular work is assumed to complete.
Internal Audit – is an Audit conducted within the Organization or Project. An audit is: “A systematic, independent, and documented process, for obtaining audit evidence and evaluating it objectively to determine the extent to which audit criteria are fulfilled.” Audits are used to gather facts and determine the degree to which requirements are being met.
The organization shall conduct internal audits at planned intervals to provide information on whether the quality management system:
a) conforms to:
1) the organization’s own requirements for its quality management system;
2) the requirements of this International Standard;
b) is effectively implemented and maintained.
ISO Certification - ISO certification certifies that a management system, manufacturing process, service, or documentation procedure has all the requirements for standardization and quality assurance. ISO (International Organization for Standardization) is an independent, non-governmental, international organization that develops standards to ensure the quality, safety, and efficiency of products, services, and systems.
Inspection and Test Plan (ITP) - is the master document that controls the quality of the project requirements. The ITP must be in place and agreed by all concerned parties prior to the commencement of any construction activities.
The requirements of the ITP must identify the following:
The quality targets to be achieved in relation to the customers projects technical, specification and contractual requirements.
The specific assignments and responsibilities of the involved inspection parties.
The specific procedures, methods and work instructions to be applied
Reference to inspection check sheets for each construction discipline
Key Performance Indicator (KPI) – Key Performance Indicators (KPIs) are the critical (key) indicators of progress toward an intended result. KPIs provides a focus for strategic and operational improvement, create an analytical basis for decision making and help focus attention on what matters most. KPIs can be used to:
Monitor costs.
Track progress.
Assess client satisfaction.
Identify strengths and weaknesses.
Compare performance across and between projects.
Assess specific areas of a project such as sustainability, safety, waste management, etc.
Laboratory Testing – is a testing of construction materials in an independent / Third Party laboratory to determine if the materials are in compliance with the design criteria, specifications, and referenced industry standards.
Method Statement – is a step wise statement or method described to perform a certain activity or operation. It can be in the form of a flowchart or a written step wise guide.
Mock-up Sample - is a physical sample of some kind that’s meant to represent a portion of the finished construction project.
Some common mockups are as follows:
Samples: Handheld, physical samples of a material or finished product that represents the final product.
In-Situ: A small amount of work that’s built onsite ‘in-situ‘ for the purpose or review and discussion. This can include samples of caulking, paint or finished product that’s installed where they will eventually be.
Table Mockup: These mockups are built to illustrate the details of a finished building component, including fabrication and assembly details. An example may be a table-sized section of a roof that illustrates the finished surface and the assembly of subcomponents underneath it.
Performance Mockup: These mockups are meant to test how a ‘prototype’ of the final finished work will perform compared to the performance standards for the project. This can include testing a product for it’s ability to weather correctly, stay water-tight or many other various performance criteria.
Non-Conformance Report (NCR) – are used and issued by the QA/QC engineers on site to a concerned party who deviated a plan and/or a specification of the construction project.
Preventive Action - aims to correct a potential problem. Unlike a corrective action, which fixes the root cause of a current issue, preventive actions try to address problems before they happen.
Project Quality Plan (PQP) - A PQP, sometimes referred to as a quality management plan, quality assurance plan or project quality management plan, is a project-specific quality plan that describes the activities, standards, tools and processes necessary to achieve quality in the delivery of a project.
Quality Management System (QMS) - is defined as a formalized system that documents processes, procedures, and responsibilities for achieving quality policies and objectives. A QMS helps coordinate and direct an organization’s activities to meet customer and regulatory requirements and improve its effectiveness and efficiency on a continuous basis.
Quality Assurance (QA) - Quality assurance can be defined as "part of quality management focused on providing confidence that quality requirements will be fulfilled." The confidence provided by quality assurance is twofold—internally to management and externally to customers, government agencies, regulators, certifiers, and third parties. An alternate definition is "all the planned and systematic activities implemented within the quality system that can be demonstrated to provide confidence that a product or service will fulfill requirements for quality."
Quality Control (QC) - Quality control can be defined as "part of quality management focused on fulfilling quality requirements." While quality assurance relates to how a process is performed or how a product is made, quality control is more the inspection aspect of quality management. An alternate definition is "the operational techniques and activities used to fulfill requirements for quality."
Quality Policy - A quality policy is a brief statement that aligns with your organization’s purpose and strategic direction, provides a framework for quality objectives, and includes a commitment to meet applicable requirements (ISO 9001, customer, statutory or regulatory) as well as to continually improve.
Records – A record of Project documents such as drawings, specifications, test reports, correspondence or other contract documents in any format, including those which are stored electronically, relating to the project.
Reject – Any work or product identified during inspection which does not meet the acceptance criteria or non-conforming product that is beyond repair.
Rework – the act of redoing or correcting work that was not done correctly the first time and prevalent on construction job sites.
Root Cause Analysis – is defined as a collective term that describes a wide range of approaches, tools, and techniques used to uncover causes of problems
Snaglist – also called Punchlist, is a document or form issued to contractors and subcontractors towards the end of their project or phase of work (usually a couple of weeks depending on the scale and scope of the works) which outlines and describes the minor defects or omissions which arose during the course of work, and which need to be rectified before that party can consider their work complete.
Standard Operating Procedure (SOP) - are documented processes that ensure processes, services and products are delivered with the best practices consistently.
Specification - are details within a construction service contract that outline all the important aspects necessary for project fulfillment. Throughout the course of project completion, contractors and construction crews may use specifications as a reference for any questions that arise and to ensure the correct fulfillment of each project requirement.
Specifications often include information about:
The scope of work
The materials to be used in the project
The timeline and important project milestones
Methods of installation
Quality of workmanship
Testing requirements
National and state safety standards
Statistical Analysis - is the process of collecting, analyzing, and monitoring data to improve capital project outcomes, reduce risks, and uncover critical insights with the help of real-time data and automated construction reports, consolidated from multiple sources.
Submittal Forms - A submittal refers to the written and/or physical information provided by a responsible contractor (i.e., contractors and subs) to the general contractor. This information is submitted to the design team for approval of equipment, materials, etc. before they are fabricated and delivered to the project. Submittals can be presented in various formats, such as shop drawings, cut sheets on equipment, and material samples. Submittals are required primarily for the architect and engineer to verify that the correct products and quantities will be installed on the project in compliance with the design documents/contract documents.
Test Reports – is a document or form which serves as proof that the design details and specs were followed correctly and that a responsible third party witnessed critical stages of the process as well as validated its integrity.
Third Party Inspection – is the inspection and testing activities by a third party individual or organisation who is performing with the purpose of certifying compliance of purchased or manufactured products, or services to the international standard, code, and customer technical specifications during and after manufacturing. The Third Party Inspection people or organisation provides technical control, testing and inspection, assessment, and approval services who must not be involved in design, procurement, fabrication, construction and installation.
Traceability - is the process of ensuring that the materials that make up all the parts on a finished product have records spanning back to their production.
References:
The Quality Improvement Handbook (Second Edition) by ASQ
asq.org
integrated-standards.com
civilmint.com
ISO 9000:2005
qaqcconstruction.com
www.meadmetals.com
solvepmproblems.com
www.qualityengineersguide.com
support.procore.com
sitemate.com
Comentários