Types of Concrete used in Construction
- raimondpsantos
- Feb 8, 2022
- 8 min read
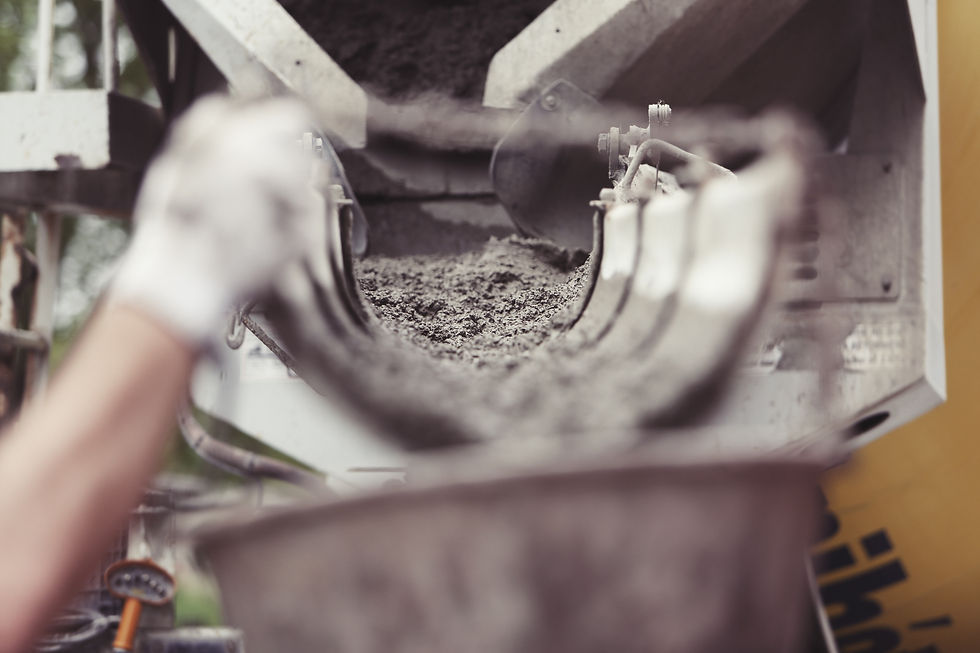
Concrete in construction is a structural material consisting of a hard, chemically inert particulate substance, known as aggregate (usually sand and gravel), that is bonded together by cement and water.
There are different types of concrete based on its usage and application as follows:
1. Normal Strength Concrete - This concrete combines all the basic ingredients — concrete, sand and aggregate — using the 1:2:4 ratio. This produces normal strength concrete. It takes about 30 to 90 minutes to set, but this is dependent on the weather conditions at the concrete site and the cement’s properties.
It’s normally used for pavements or buildings that don’t need high tensile strength. It is not very good for many other structures since it doesn’t withstand the stresses created by wind loading or vibrations very well.

2. Plain or Ordinary Concrete - This is another concrete that uses the common mix design of 1:2:4 with its components of cement, sand and aggregates. You can employ it to make pavement, footpaths or buildings where there is not a high demand for tensile strength. It faces the same challenges as normal strength concrete — it doesn’t stand up very well to vibrations or wind loading. The durability rating of this kind of concrete is very satisfactory.

3. Reinforced Concrete - This form of concrete is widely used in industry and modern construction. The strength of reinforced concrete is aided by placing wires, steel rods or cables in the concrete before it sets. A more familiar name for these items is rebar. Lately, people have used fibers to reinforce this concrete.
These reinforcements resist tensile forces while the concrete itself helps resist compressive forces. They create a strong bond and, as a result, the two materials resist a variety of applied forces. In essence, they become a single structural element.

4. Prestressed Concrete - Many large concrete projects use prestressed concrete units. Prestressed concrete is created using a special technique. Like reinforced concrete, it includes bars or tendons. But these bars or tendons are stressed before the actual application of the concrete.
When the concrete is mixed and placed, these bars are placed at each end of the structural unit where they are used. When the concrete sets, this unit is put into compression.
This process makes the lower section of the unit stronger against tensile forces. It requires heavy equipment, however, and skilled labor. Normally, prestressed units are created and assembled on-site. Prestressed concrete is used to build bridges, heavy loaded structures or roofs that have long spans.

5. Precast Concrete - This concrete is created and cast in a factory according to exact specifications. Precast concrete units are then transported to the site and assembled.
You frequently see these units transported to worksites as you drive on highways. Precast concrete is used for:
Concrete blocks
Precast walls
Staircase units
Poles
The advantage of using precast concrete is its speedy assembly. Since the units are manufactured in a factory, they are of very high quality.

6. Lightweight Concrete - Lightweight concrete is any kind of concrete that has a density of less than 1920kg/m3. Lightweight concrete is created by using lightweight aggregates. Aggregates are ingredients that add to the density of the style of concrete. These lightweight aggregates include natural materials like scoria or pumice, artificial materials like clays and expanded shales or processed materials like vermiculite and perlite. Its most important property is that it has very low thermal conductivity.
Common uses for lightweight concrete include creating long spanning bridge decks and building blocks. It can also be used to protect steel structures.

7. High-Density Concrete - High-density concrete has a very specific purpose. It is frequently used in the construction of atomic power plants. The heavyweight aggregates used in the creation of high-density concrete help the structure resist radiation.
Crushed rocks are normally used. Barytes, a colorless or white material that consists of barium sulfate and is the principal ingredient in barium, is the crushed rock most often employed.
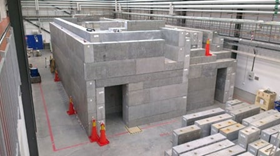
8. Air-Entrained Concrete - Some types of concrete hold billions of microscopic air cells in every cubic foot. These tiny air pockets relieve the internal pressure on the concrete. They provide tiny chambers where water can expand when it freezes.
The air is entrained in the concrete by adding various foaming agents such as alcohols, resins or fatty acids during the mixing process. This must be done under careful engineering supervision since the concrete is mixed on the job site. The entrained air adds up to about 3% to 6% of the volume of the concrete. Almost all concrete used in a freezing environment or where there are freeze-thaw cycles is air-entrained.

9. Ready-Mix Concrete - Concrete prepared and bathed in a centrally located plant is known as ready-mix concrete. This concrete is mixed as it is transported to the site in the familiar cement trucks seen often on roads and highways. Once the trucks reach the worksite, the cement can be used immediately because it does not need further treatment. Ready-mix concrete is a specialty concrete that is mixed based on specifications developed with great precision.
Creating ready-mix concrete requires a centralized location where the concrete can be prepared. These locations need to be placed at an adjustable distance from the worksite. If the concrete takes too long to reach the worksite, it will be of no use. In most cases, the worksite to far from the preparation plant. Retarding agents are sometimes used to delay how long the concrete takes to set.
Ready-mix concrete is preferred to concrete mixed on-site because the mixture has higher precision and having the concrete ready to pour reduces confusion on the worksite. Ready-mix concrete can be used for buildings, roadways, walls and more.

10. Volumetric Concrete - This concrete was created as an alternative to ready-mix concrete to address the problem of long distances between the concrete plant and construction sites. It requires specialized trucks known as volumetric mobile mixers. They carry the concrete ingredients and the water that will be mixed at the construction site.
Volumetric concrete is extremely useful when a builder requires two different kinds of concrete mix at a single site. Since the concrete can be mixed and delivered as needed, it allows one truck to produce two different mixes of concrete. It is very useful on large sites, basement constructions and multi-projects where you need different types of concrete.
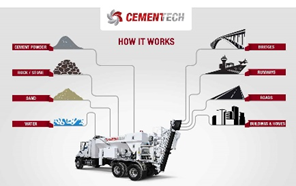
11. Decorative Concrete - Decorative concrete creates visually and aesthetically appealing concrete mixes. Decorative concrete can go through several processes, such as:
Coloring
Molding
Polishing
Etching
Applying decorative toppings
It is ideal for any project in which you want to make an aesthetic statement. It’s also a great way to add a bit of “personality” to dull surfaces or structures. For instance, swimming pools and flooring can make great use of decorative concrete.
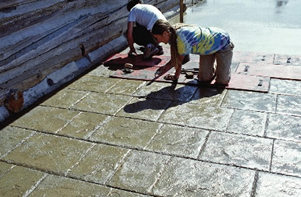
12. Rapid-Set Concrete - In a hurry? Then you need rapid-set concrete. It’s ideal when you’re short on time to complete a project. It has faster set times and is very resistant to low temperatures, so it can be used any time of the year. It’s especially useful in winters when the cold weather does not allow you to use many other kinds of concrete.

13. Smart Concrete - This is the concrete technology of the future. It offers a different way to monitor the condition of reinforced concrete structures. Short carbon fibers are added to the concrete using a conventional concrete mixer. This affects the electrical resistance of the concrete when it encounters strain or stress. This kind of concrete can be used to detect possible problems before the failure of the concrete.
It is very good at sensing tiny structural flaws. While not widely available yet, it promises to be the building material of the future for cities that face a repeated earthquake risk. Smart concrete allows engineers in those cities to check the health of structures after earthquakes, providing a far better assessment of their condition than a visual inspection.
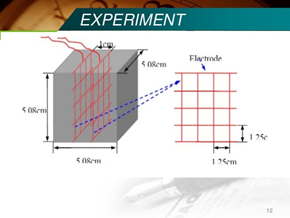
14. Pervious Concrete - This is one of the most common kinds of concrete used to build roads and pavements. It is designed to deal with the problems of stormwater runoff and pools of water and puddles on roadways or airport runways.
Other concrete absorbs water. Roadways that use pervious concrete have fewer problems with hydroplaning, tire spray and snow buildup. It also reduces the need for curbing and storm sewers.
It is composed of a mixture of cement, water and coarse aggregates. It contains no sand, which creates an open-scale, porous structure. This allows water to pass through the layers more easily. Some kinds of pervious concrete will pass several gallons of water through its surface per minute.

15. Pumped Concrete - If you’ve ever wondered what types of cement mixtures used in the flooring of a very tall building are, the answer is probably pumped concrete. The secret to pumped concrete is that it is very workable, so it can be conveyed easily via a pipe to an upper floor. This pipe will be a flexible or rigid hose that discharges the concrete to the required area.
Pumped concrete can also be used:
· To create superflat floors on lower structures
· In construction projects like roadways and bridges
· For more personal items, like swimming pools
It is a reliable, efficient and economical way to apply concrete and is often the only way that concrete can be placed in certain locations. Very fine aggregates are used in pumped concrete. The finer the aggregate used in the mix, the freer the concrete flows from the pipe.
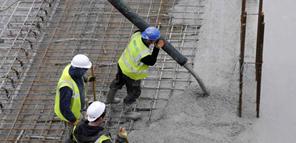
16. Limecrete - This concrete uses lime instead of cement, along with lightweight aggregates like glass fiber or sharp sand. It’s mainly used for the construction of floors, vaults and domes. Limecrete has many environmental benefits because it is so easily cleaned and is renewable. It can also be used with radiant floor heating.

17. Roll Compacted Concrete - It’s a familiar sight on many American highways — a heavy roller compacting a layer of concrete. Roll-compacted concrete is a strong, dense concrete used on heavily trafficked highways with vehicles that carry large loads. This concrete emits fewer emissions during the production process, which benefits the environment.
Roll compacted concrete can be found in roadworks, airport runways, car parks, pavements and industrial servicing.
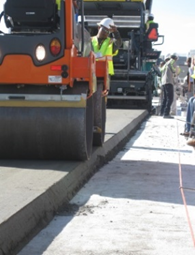
18. Glass Concrete - Another, more modern form of concrete, glass concrete features the use of recycled glass. This form of concrete is used when aesthetic appeal is an important element in the design of the concrete.
Commonly used in the large-format slabs found in flooring or on decorative façades, this concrete can have shining or colored glass embedded during the mixing process to give it a distinctive splash of color or sparkle.
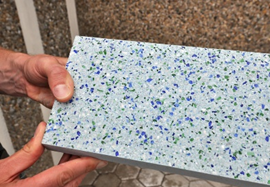
19. Asphalt Concrete - More commonly known as “asphalt” or “blacktop,” this is a form of concrete frequently used on roads, on airport runways, on highways, in parking lots, for sidewalks — basically anywhere pavement is needed. Asphalt is a dark mineral composed of a mixture of hydrocarbons called bitumens.
The desire for asphalt grew along with the automobile industry. Known for its durability, workability, skid resistance, stability, fatigue resistance, flexibility and permeability, it still requires a properly designed mixture. It is a composite mixture of aggregates and asphalt. The different mixtures of asphalt are used for different purposes.

20. Shotcrete Concrete - Shotcrete differs from other forms of concrete primarily in the way it is applied. Shotcrete is shot through a nozzle onto a frame or formwork. Since this application requires higher air pressure, the compaction process takes place at the same time as the placing.
Shotcrete can be used to repair damaged wood, concrete or steel structures. It is also commonly used when access to a work area is difficult or when formwork is impractical or cost-prohibitive.

Note:
All photos belong to their rightful owners. I claim no ownership of any content posted here unless stated otherwise.
Sources:
Dynamic Concrete Pumping Inc.
Britannica
Comments