Top Quality Gurus and their Key Contributions
- raimondpsantos
- Feb 22, 2022
- 9 min read
Updated: Feb 23, 2022
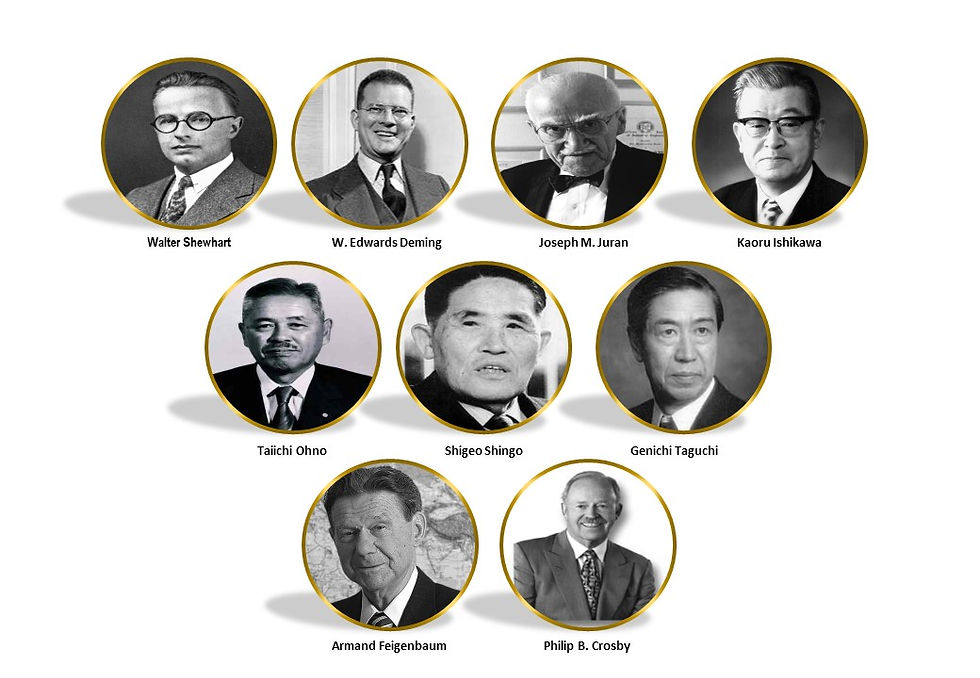
Here are some of the Top Quality Guru’s who contributed to the development of quality:
1. Walter Shewhart – He is the father of statistical quality control. He developed the Plan, Do, Check, Act (PDCA) cycle (known as “Plan-Do-Study-Act” in some circles) as well as theories of process control and the Shewhart transformation process.
Shewhart introduced the concept of control charts in the 1920s. Because of his work, several control charts monitoring a single quality characteristic of interest are referred to as Shewhart control charts.
2. W. Edwards Deming – Considered by many to be the master of continual improvement of quality, as well as their overall operation. Deming is best known for his pioneering work in Japan. Known for his Deming’s 14 points as follow:
1. Create consistency of purpose toward improvement of products and services, with a plan to become competitive and to stay in business. Decide to whom top management is responsible. 2. Adopt the new philosophy. We are in a new economic age. We can no longer live with commonly accepted levels of delays, mistakes, defective materials, and defective workmanship. 3. Cease dependence on mass inspection. Require instead statistical evidence that quality is built-in to eliminate need for inspection. Purchasing managers have a new job and must learn it. 4. End the practice of awarding business on the basis of price tag. Instead, depend on meaningful measures of quality, along with price. Eliminate suppliers who cannot qualify with statistical evidence of quality. 5. Find problems. It is management’s job to work continually on the system (design, incoming materials, composition of material, maintenance, improvement of machines, training, supervision, retraining). 6. Institute modern methods of training on the job. 7. Institute modern methods of supervision of production workers. The responsibility of foremen must be changed from sheer numbers to quality. Improvement of quality will automatically improve productivity. Management must prepare to take immediate actions on reports from foremen concerning barriers such as inherited defects, machines not maintained, poor tools, fuzzy operation definitions. 8. Drive out fear, so that everyone may work effectively for the company. 9. Break down barriers between departments. People in research, design, sales, and production must work as a team, to foresee problems of production that may be encountered with various materials and specifications. 10. Eliminate numerical goals, posters, and slogans for the workforce, asking for new levels of productivity without providing methods. 11. Eliminate work standards that prescribe numerical quotas. 12. Remove barriers that stand between the hourly worker and his right to pride of workmanship. 13. Institute a vigorous program of education and retraining. 14. Create a structure in top management that will push every day on the above 13 points.
3. Joseph M. Juran - The Father of Quality. Applied the 80/20 rule (The Pareto Principle) to quality issues; he coined the phrase “the vital few and the trivial many” to convey that a small percentage of root causes can result in a high percentage of problems or defects.
The Juran Trilogy, also known as the Quality Trilogy, consists of the three processes that together make up the overall quality management journey. The three components of the Juran Trilogy are:
Quality planning – This is effectively the design stage during which an organization establishes an understanding of its target customer’s needs, defines the features and specifications of the product or service, and devises the processes that will deliver on those needs.
Quality control – Ongoing quality control involves periodic checks and inspections, and tracking metrics to ensure the process is in control and meeting specifications. Where defects are identified, root causes need to be identified to enable corrective and preventative action.
Quality improvement – While organizations may expect to achieve incremental improvements by day-to-day means, breakthrough quality improvement involves the identification of areas where processes can be optimized, and the organized creation of beneficial change in order to attain measurably improved performance.
4. Kaoru Ishikawa - created quality circles and invented the cause-and effect diagram, also called the Ishikawa diagram. Cause-and-effect diagrams are used in problem-solving situations and in general analysis to identify factors (that is, causes) related to a problem or opportunity (That is, effect) to help the problem-solving or analysis team understand how those factors may cause the given effect, and to help the problem-solving or analysis team focus on “next steps” in process improvement.
5. Taiichi Ohno - He is considered to be the father of the Toyota Production System, which inspired Lean Manufacturing in the U.S. He devised the seven wastes (or muda in Japanese) as part of this system.
Ohno is also known for his "Ten Precepts" to think and act to win.
1. You are a cost. First reduce waste.
2. First say, "I can do it." And try before everything.
3. The workplace is a teacher. You can find answers only in the workplace.
4. Do anything immediately. Starting something right now is the only way to win.
5. Once you start something, persevere with it. Do not give up until you finish it.
6. Explain difficult things in an easy-to-understand manner. Repeat things that are easy to understand.
7. Waste is hidden. Do not hide it. Make problems visible.
8. Valueless motions are equal to shortening one's life.
9. Re-improve what was improved for further improvement.
10. Wisdom is given equally to everybody. The point is whether one can exercise it.
6. Shigeo Shingo - A leader in the fields of continuous process improvement and operational excellence, Shigeo Shingo taught thousands of engineers at Toyota the Toyota Production System, influenced the creation of Kaizen and developed the concept of the Single-Minute Exchange of Die (SMED).
The Shingo Model process improvement principles:
1. Respect Every Individual – This means treating everyone in an organization with respect and as a human being with potential. An example of this would be creating an employee development plan that allows employees to maximize their potential.
2. Lead with Humility – Leaders should seek input from others and always be willing to learn. Such leaders can create a culture where employees feel respected and energized.
3. Seek Perfection – Perfection cannot ever be achieved, but the pursuit of perfection creates a culture of continuous improvement.
4. Embrace Scientific Thinking – Experimentation, observation and a systematic exploration of ideas enables organizations to constantly improve and refine “our understanding of reality.”
5. Focus on Process – Every outcome is a function of a process. Understanding current processes and improving them leads to better outcomes. Problems usually involve processes, not people.
6. Assure Quality at the Source – Improved quality can only happen when every aspect of a process is done right the first time. Errors should be detected and corrected at the point of creation.
7. Flow & Pull Value – Organizations create value for customers when they respond to real demand and create a continuous and uninterrupted flow. Anything that disrupts continuous flow of value is a waste.
8. Think Systemically – Only understanding every part of a process and how they interconnect can lead to better decision-making and improvements.
9. Create Constancy of Purpose – An organization’s purpose and goals should be clearly communicated and understood by all. There needs to be “an unwavering clarity” on why the organization exists, where it is going and how it will get there.
10. Create Value for the Customer – This is the foundation of everything. All value in an organization must be created by defining what a customer wants and what they are willing to pay for. Not doing so makes a company unsustainable.
7. Genichi Taguchi - Taguchi is famous for his pioneering methods of modern quality control and low-cost quality engineering. He is the founder of what has come to be known as the Taguchi method, which seeks to improve product quality at the design stage by integrating quality control into product design, using experiment and statistical analysis. His methods have been said to fundamentally change the philosophy and practice of quality control.
During the product design and production engineering phases, Taguchi set out three steps that must be followed.
1. System design: This may involve the development of a prototype design and will determine the materials, parts, and assembly system to be used. The manufacturing process has also to be considered.
2. Parameter design: Taguchi's parameter design aimed to find the most cost-effective way of controlling noise. Taguchi process and design improvements are gained by identifying easily controllable factors and settings that minimise performance variation. Controllable factors are design factors that a designer can set or easily adjust. The specified value becomes the signal. Uncontrollable factors are noise, or external variations, and a higher signal to noise ratio means better quality. Taguchi found that if controllable factors were set at optimal levels, the product would be robust to external changes. This was achieved through parameter design applied at the design (offline) stage to reduce or remove the effect of noise factors, and design in robustness. Experiments were designed using orthogonal arrays which (rather simply described) were a series of rows and columns allowing the effects of different factors to be extracted, and separated out. Taguchi was not the inventor of the orthogonal array, but this type of experimentation moved away from the traditional approach of testing one factor at a time and, instead, tested many factors at the same time. His new approach dramatically reduced the number of experiments and prototypes required and, in consequence, costs were much lower. He developed various experimental designs which allowed the variability of the noise factors on each controllable factor setting to be simulated. The settings that minimised variability could then be determined.
3. Tolerance design: If parameter design failed, Taguchi suggested using tolerance design to identify the most crucial noise factors. Tolerances could be reassigned so that the overall variability was reduced to acceptable levels.
8. Armand Feigenbaum – He developed the “Total Quality Control” concept while concurrently at GE. He established the principles of Total Quality Management (“TQM”), the approach to quality and profitability that has profoundly influenced management strategy and productivity in the competition for world markets in the United States, Europe, Asia, Latin America and the Middle East. He wrote, “Total quality control is an effective system for integrating the quality development, quality maintenance, and quality improvement efforts of the various groups in an organization so as to enable production and service at the most economical levels which allow full customer satisfaction.”
The elements of total quality to enable a totally customer focus (internal and external)
Quality is the customers perception of what quality is, not what a company thinks it is.
Quality and cost are the same not different.
Quality is an individual and team commitment.
Quality and innovation are interrelated and mutually beneficial.
Managing Quality is managing the business.
Quality is a principal.
Quality is not a temporary or quick fix but a continuous process of improvement.
Productivity gained by cost effective demonstrably beneficial Quality investment.
Implement Quality by encompassing suppliers and customers in the system.
9. Philip B. Crosby - was a legend in the discipline of quality. A noted quality professional, consultant, and author, he is widely recognized for promoting the concept of "zero defects" and for defining quality as conformance to requirements.
Crosby was recognized by corporations around the globe as a "guru" of quality management, nd a business philosopher and innovator who changed the way organizations seek to achieve greater efficiency, reliability, and profitability.
Crosby’s 14 Steps for Improvement
1. Management Commitment - Top-level view on quality shown to all employees.
2. The Quality Improvement Team - To pursue the quality regime throughout the business.
3. Quality Measurement - Analysis of business quality performance in a meaningful manner, for example late deliveries, budgeted to actual sales/deliveries/costs/etc. Keep it simple for all to understand.
4. The Cost of Quality - Make sure everyone in the business understands the need for a quality system, and the costs to the business if there is no quality system in place.
5. Quality Awareness - Again make everyone in the business aware of the impact of quality systems.
6. Corrective Action - Ensure a system is in place for analyzing defects in the system and applying simple cause and effect analysis, to prevent re-occurrence.
7. Zero Defects Planning - Look for business activities to which zero defect logic should be applied.
8. Supervisor Training - Get your supervisors trained in both quality logic and zero defect appreciation which they can apply to their business activities.
9. Zero Defects Day - A quality event by which all members of the effected section become aware that a change has taken place.
10. Goal Setting - Once a change has been implemented in a section of the business, the next step is to get the employees and supervisors in that section to set goals for improvement to bring about continuous improvement.
11. Error Cause Removal - Communication process by which management are made aware that set goals are difficult to achieve in order for either the goals to be reset or help given by management to achieve the goals.
12. Recognition - Management must recognize the employees who participate in the quality schemes.
13. Quality Councils - Using both specialist knowledge and employee experiences to bring about a focused approach to business quality regime.
14. Do It Over Again - Continuous improvement means starting from the beginning again and again.
References:
The Certified Quality Engineer Handbook (3rd Edition)
Wikipedia
deming.org
www.feigenbaumfoundation.org
Note: All photos belong to their rightful owners. I claim no ownership of any content posted here unless stated otherwise.
Kommentarer